Carbon Fiber / Epoxy Composites: Ideal Materials for Orthopedic Prosthetics.
Melville beautifully describes the tock-tock-tock sounds made by Captain Ahab’s wooden leg as he paces on the deck of the whaler Pequod, chasing the great white whale, Moby Dick! However, artificial legs, or orthopedic prosthetics as they are nowadays called, have undergone fundamental changes since the time of Captain Ahab.
The greatest leap in technology occurred in the last 5 to 10 years with the use of carbon fiber composites and light-metal alloys in the production of prostheses. Modern prosthetic devices (Figure 2) help tens of thousands of individuals to at least partially compensate for their missing limbs and lead a high quality life. Some of the users engage in sport activities, even break records.
Why are carbon fiber / epoxy composites were so successful in the production of prosthetics? What is the determining factor: their attractive look, price, simple manufacturing process, or their technical superiority as suggested by material sciences? To answer this question, we have to focus on the required specifications of prosthetics and on the properties of carbon / epoxy composites.
1. Modern Molding Techniques:
The key feature of modern prosthetics is the fact that they can be custom-made to match the height, weight, and muscular structure of the individual. It is impossible to give the prosthesis the desired shape using a manufacturing process that involves machining. Thus, the material used has to be suitable for the molding manufacturing technology. The greatest advantage of fiber composites is that they lend themselves to the production of deep components with thin walls and compound curves. Using split dies in combination with resin transfer molding and prepreg methods, it is possible to produce any kind of complex structures
2. Varying Mechanical Properties Along the Component:
A prosthesis is expected to fully replicate the functions of the natural organ it replaces. Thousands of years of evolution have turned human muscles and bones into perfect structures with a high resistance / weight ratio and varying properties at different regions. Nature is everything but generous: It doesn’t allow any part in our body to be stronger and heavier than necessary. When we examine a bone, we see that different regions are not identical but have different collagen, hydroxyapatite and pore ratios. This phenomenon, referred to as the Wolff's law in medicine, stipulates that bones have a higher density and strength at high-stress regions (e.g. tips) while low-stress regions have a lower density and strength. The tip of the tibia has 50% higher density and compressive strength. Due to the long time spent in zero gravity, the bones of astronauts become weaker. With recent advances in the molding methods of composite materials, it is possible to obtain varying levels of strength and modulus in different regions of a component. Especially using resin transfer molding and modern fiber lay-up (tow placement) methods, varying wall thicknesses in different parts can be obtained with a high accuracy. Thus, it is possible to produce components with varying strengths in different regions that mimic nature as stipulated by the Wolff's law
3. High Specific Strength:
In warm-blooded animals, muscles and tendons facilitate body’s movements while bones and joints are the weight-bearing components. Prosthetics that are currently approved by medical authorities and routinely used in practice take over the function of the bones. Active prosthetics with an internal power sources are still in the stage of development. A prosthesis that replaces a bone has to have a mechanical strength similar to the native bone. Currently available carbon / epoxy composites easily produce a tensile strength of 700 MPa and a modulus of elasticity of 70 GPa. Considered together with its density of 1.6 g/mL, the very high specific strength of this material becomes more evident. In addition to its tensile strength, a high compressive strength and fracture toughness contribute to the superior qualities of this material. There are also other candidates for the production of prosthetics. Conventional wood, fiberglass/polyester composites, glass and carbon fiber / thermoplastic composites, metals and their alloys, or ceramics may also be used in prosthetics. Figure 4 shows a comparison between the various candidate materials and native bone. Carbon / epoxy composite most closely resembles native bone with regard to absolute strength, modulus, and fracture toughness.
4. Ideal Weight Distribution:
The specific strength of the aforementioned carbon / epoxy composite is so high that it is possible to produce a prosthesis that has the same strength as a natural leg, but is 60% lighter at the same time. The first carbon fiber prosthetics produced were indeed very light. Thanks to this new material, a total leg prosthesis could weigh as few as 2 to 3 kilos. The leg of a man weighing 80 kilo, however, weighs around 13 to 14 kilos. Experiments in the 70’s have shown that these ultra-light prosthesis were not practical at all. Interfering with the optimum weight distribution of the human body produced poor results. Changing the weight distribution of the human body makes activities like sitting, bending, or reaching up more difficult. This indicates that rather than the total weight of the prosthesis, it is the weight distribution and the resulting angular momentum that matters. Especially for lower limb prosthesis, adding lead weights to a light component near the knee region facilitates the movements of the joint. It was also discovered that the weight of the arm prostheses must be approximately the same as what the muscles are accustomed to move throughout their lifetime. Fine tuning by attaching a weight to the most appropriate location in the prosthesis, spreading out or focusing this weight at one point is extremely simple with carbon fiber / epoxy composite, which makes this material very successful in the manufacture of prosthetics.
4. Hygiene: In addition to a high strength, any material that is used in a prosthesis must be easy to clean, non-hygroscopic, resistant to corrosion and to bacterial and fungal infections, UV-resistant, not sensitive to sweat and salt, and cosmetically acceptable. Following curing and washing, epoxy resin does not irritate the human skin and is non-allergic. Accidental exposure of the skin to the prosthesis does not cause any harm. Carbon composites exhibit all the desired properties.
5. Elastic Properties:
An important characteristic of proteins found in muscles and tendons called myelin and elastin is that they act like a spring in steady state. Over thousands of years, elastin, the main building block of tendons, has evolved into the perfect “Hookean Solid”. A material that exhibits a linear relationship between the applied stress and the resulting strain is referred to as a “Hookean Solid”. Examples of such materials include a steel spring or a rubber band. The elastin in the Achilles tendon of a kangaroo acts like a perfect spring and enables the animal to run long distances using relatively small amount of energy. Each time the kangaroo hits the ground, there is an elastic collision and nearly all of the kinetic energy is transformed
into potential energy. Thus, only a small amount of additional energy is required for the next jump. When walking or running, humans make use of the same kinetic/potential energy transformation. The linear zone (characteristic of Hooke solids) that is observed at the beginning of the 3-point bend testing of glass, aramid, and carbon fiber composites is most pronounced in carbon / epoxy composites. Among these three different composite materials, carbon fiber composite agrees best with the Hooke’s law in case of small deformities. I believe that this is the main reason why carbon / epoxy composites are the material of choice for prosthetics.
6. Fatigue Strength:
Another requirement of a prosthetic material is fatigue strength. It is obvious that the load a prosthesis is subject to does not remain constant, but changes with every step, with the device continuously bending and returning to its original shape. Every known material loses some of its strength upon repeated bending for a certain number of cycles, ultimately leading to component failure. Naturally, a gradual reduction in the strength and a short lifespan is not acceptable for a prosthetic device. The lifespan of the aluminum prosthetics from the 60’s was only 1 year. Cracking of the polymeric matrix, fiber rupture, delamination of the layers, and separation at the matrix/fiber interface are the four distinct modes of failure that are observed with composites upon repeated bending. The separation at the fiber / matrix interface has the greatest impact on the life of the component. The plot in Figure 5 shows the degree of strength loss as a result of fatigue for different materials. The high residual strength of carbon fiber / epoxy composite following exceptionally high number of stress cycles can be seen on this chart. The use of carbon fiber / epoxy composites in aerofoils, wind turbine blades, and Formula 1 racing cars speaks for the extremely high fatigue strength of this material.
7. Conclusion:
When selecting a material for the production of prosthetics, carbon fiber / epoxy composites stand out as the material of choice due to a number of factors including their tensile strength and compressive strength, modulus, impact resistance, fatigue resistance, specific weight, ease of manufacturing, hygiene, and aesthetic factors. Tens of thousands of people all around the world live a better and more fulfilling life thanks to carbon composite prosthetics.
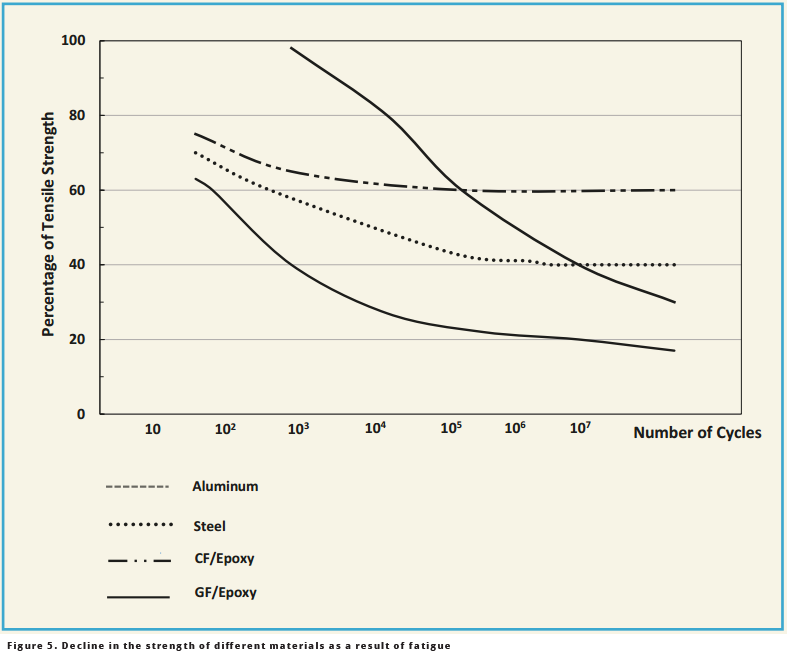