The Importance of Sandwich Structures and the Development of Kordsa’s First Composite Sandwich Panel
INTRODUCTION
Saving energy or reducing its consumption is among the primary aims of engineering today. Innovations in the field of materials science offer opportunities for producing lighter and stronger structures with reduced energy consumption. Among the most popular materials for this purpose are “Composite Materials”. Instead of having single constituents, these have at least two different constituents, which when combined preserve the benefits of the separate constituents. While one constituent (reinforcement) provides strength and stiffness for the overall material system, the other constituent (matrix) is used to hold the reinforcement together. Fibre-reinforced polymer composite materials are the most important types of all.
The most significant property of fibre-reinforced polymer composite materials is their “high-strength to low-density” nature. A comparison of tensile strengths and densities of composites with different materials can be seen in Figure 1 (Ashby’s material chart). It is these characteristics that have made polymer composites an essential component for the aviation and aerospace industry over the last 40 years. Nowadays, at least 50% of any aeroplane consists of polymer composites. An example of the exterior of a Boeing B787 is shown in Figure 2.
The usage of composites is not limited to the outer regions of an aeroplane. 70% of the interior parts consist of polymer composites as well. By founding the Composites Center of Excellence (CTCE) in 2016, KordSA made an important contribution to increasing the use of composites and thus generating the kind of statistics we see in Figure 2. Now, however, we seem to be moving on to a new phase, with the development and widespread use of “Composite flat sandwich panels”
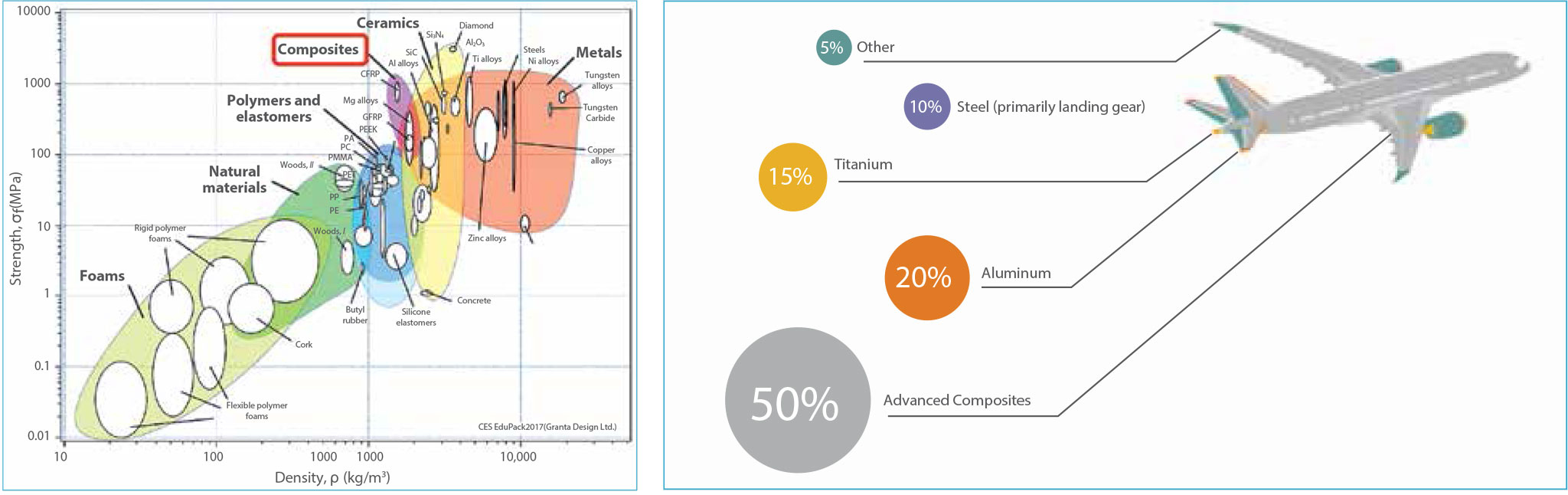
Figure 1 : Comparison of materials with respect to strengh vs. destiny
Figure 2 : Percentage of materials used in outer regions of Boing B787 aeroplane.
COMPOSITE SANDWICH PANELS
Through CTCE, Kordsa is engaged in producing large composite flat sandwich panels for the cabin interior of a commercial aeroplane, including elements such as galleys, lavatories, crew rest-spaces, floors and sidewalls. But what is a composite sandwich panel? As mentioned before, a fibre-reinforced polymer composite material can provide considerable strength owing to its low density. Despite its high tensile strength properties, though, a composite cannot sustain such strong loads when being bent. A simple “solid mechanics” rule, shown in Figure 3, states that the sustained bending stress is related to its moment of inertia (I) which is also related to its thickness (h). If the thickness of a structure is increased, the magnitude of bending stress under a load decreases, as the equations in Figure 3 illustrate. However, it is not easy to produce thick composite materials, since this involves high cost and considerable time. In addition to this, exothermic reactions are more likely to happen in thick composites and this can have detrimental effects on the physical and chemical properties of the material. For this reason, a different type of reinforcement is required to increase the bending load bearing capacity of these fibre-reinforced polymer composite materials.
Composite sandwich structures are special types of composite materials that are produced by inserting a thick, lightweight core between two thin, stiff and strong polymer composite facesheets. Also, an adhesive material is used to join the facesheet to the core. Since the thickness of the structure increases, its bending load bearing capacity is also enhanced, as is evident from the formulations shown in Figure 3.
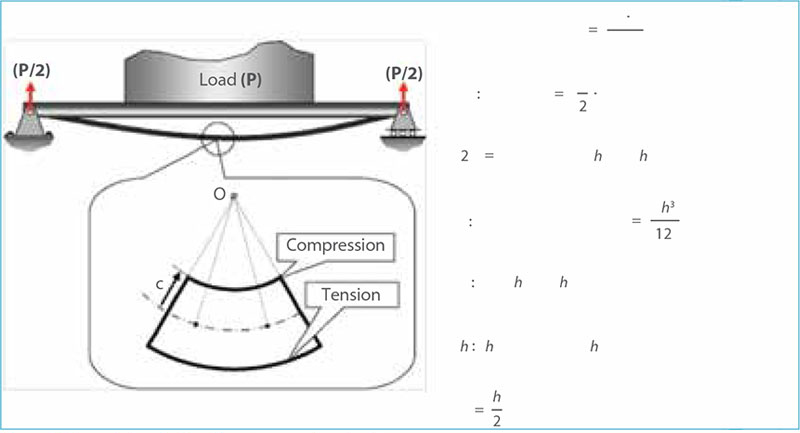
Figure 3 : Formulation for bending stress under a load.
There are various options for designing a sandwich structure. Any variation in facesheet, core type and overall geometry will have a great impact on the general structural properties. Examples of different composite sandwich panels are shown in Figure 4. While the first two types are used for outer regions of an aeroplane, the third type is highly appropriate, indeed invaluable, for the interior of an aeroplane. This is KordSA’s new “honeycomb” composite sandwich panel.
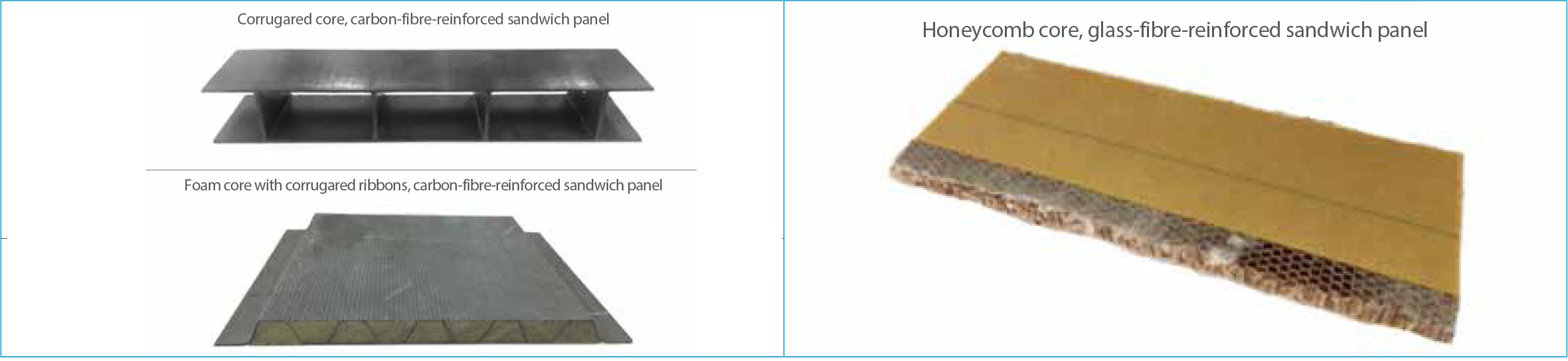
Figure 4 : Different types of coposite sandwich panels
KORDSA’S NEW HONEYCOMB SANDWICH PANEL TECHNOLOGY
Manufacture of Sandwich Panels
The Composites Reinforcement Business Unit has been producing composite sandwich panels since 12th June 2018. The primary use of these panels is in the construction of galleys of commercial aeroplanes. Since the panels will be used for interior structures, their fire progression and smoke/toxic gas emission properties need to be very low. Because of this, the product is made of glass fibre-reinforced phenolic facesheets and nomex honeycomb core. Phenolic is a flame retardant resin type and the honeycomb is an aerospace-grade aramid fiber made from Nomex® paper, which is also phenolic-coated. The honeycomb cells are hexagonal shaped and 3.2 mm in size. The schematic view of the fabrication process is shown in Figure 5.
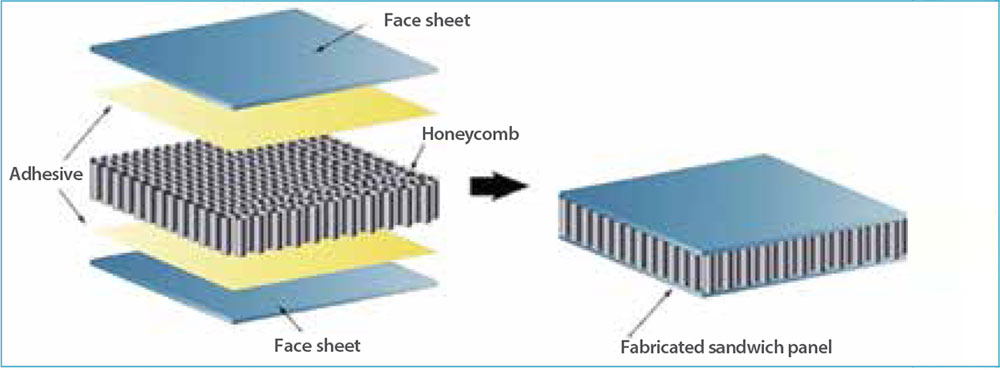
Figure 5 : Schematic view of a composite sandwich panel.
Test Results
The extensive product development period for the composite sandwich panels lasted from 12 June 2018 to the beginning of December 2018. Two different panel types were produced. While one is 10mm thick, the second has a thickness of 22mm. A total of 30 panels were produced and tested with 8 different tests (2 fire tests and 6 mechanical tests). The test list is presented in Figure 6. These tests were applied in two perpendicular directions, namely longitudinally (L) and transversally (W), in accordance with the geometry of the honeycomb cells, as illustrated in Figure 6. Different production process parameters were tested and an optimization study was carried out to determine the most effective process cycle in terms of cost, time and mechanical strength properties.
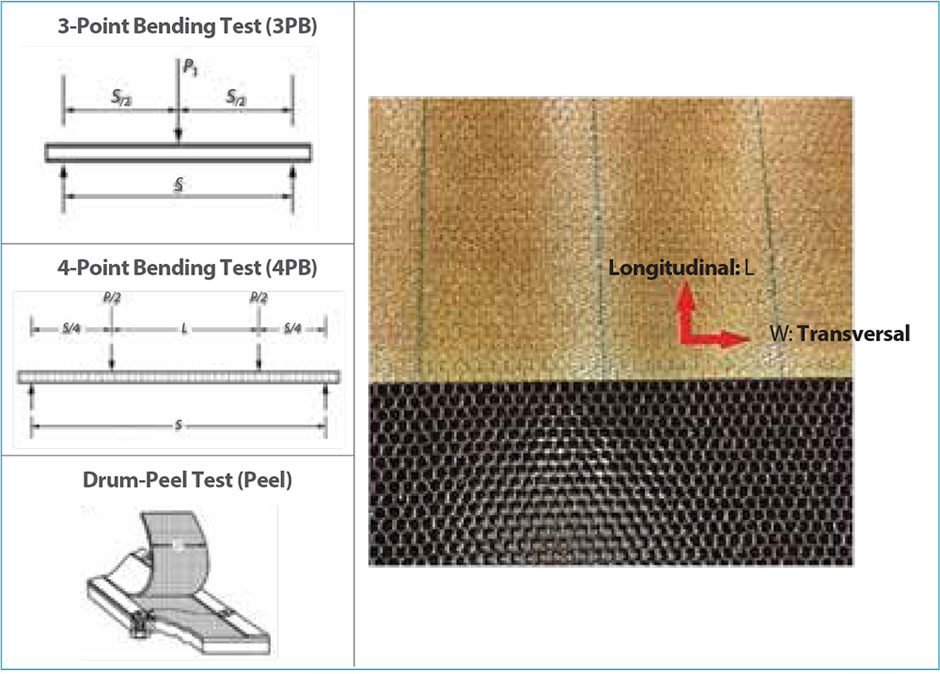
Figure 6 : Test and direction configurations
The production process parameters were fixed at the beginning of December 2018. Since then, KordSA has been able to manufacture flame-retardant composite sandwich panels that have greater mechanical properties than those of the similar, commercially available composite sandwich panels produced by a leading brand. To highlight the reliability of the product development process, it should suffice to mention that, while 6 specimens are usually regarded as sufficient for determining the mechanical properties of a product in terms of required testing standards, KordSA has tested no less than 18 specimens from different regions of a sandwich panel. This is necessary to spot the “worst scenarios” and to trace the consistency and homogeneity of mechanical properties through the entire product. A comparison of the mechanical properties of KordSA’s panels with the leading brand’s commercially available product is shown in Figure 7. Figure 8 presents the distribution of test results from various regions of a panel, with different colors representing the specimens of each test.
The test results in Figure 7 attest to the success of the product. KordSA’s composite sandwich panels can bear greater bending than can the sandwich panels of the leading brand and can withstand peel loads in either direction. In addition, Figure 8 presents the traceability of the maximum loads of the test specimens in different regions of the panel. All these results provide insight into the mechanical behavior of Kordsa’s new composite sandwich panel product.
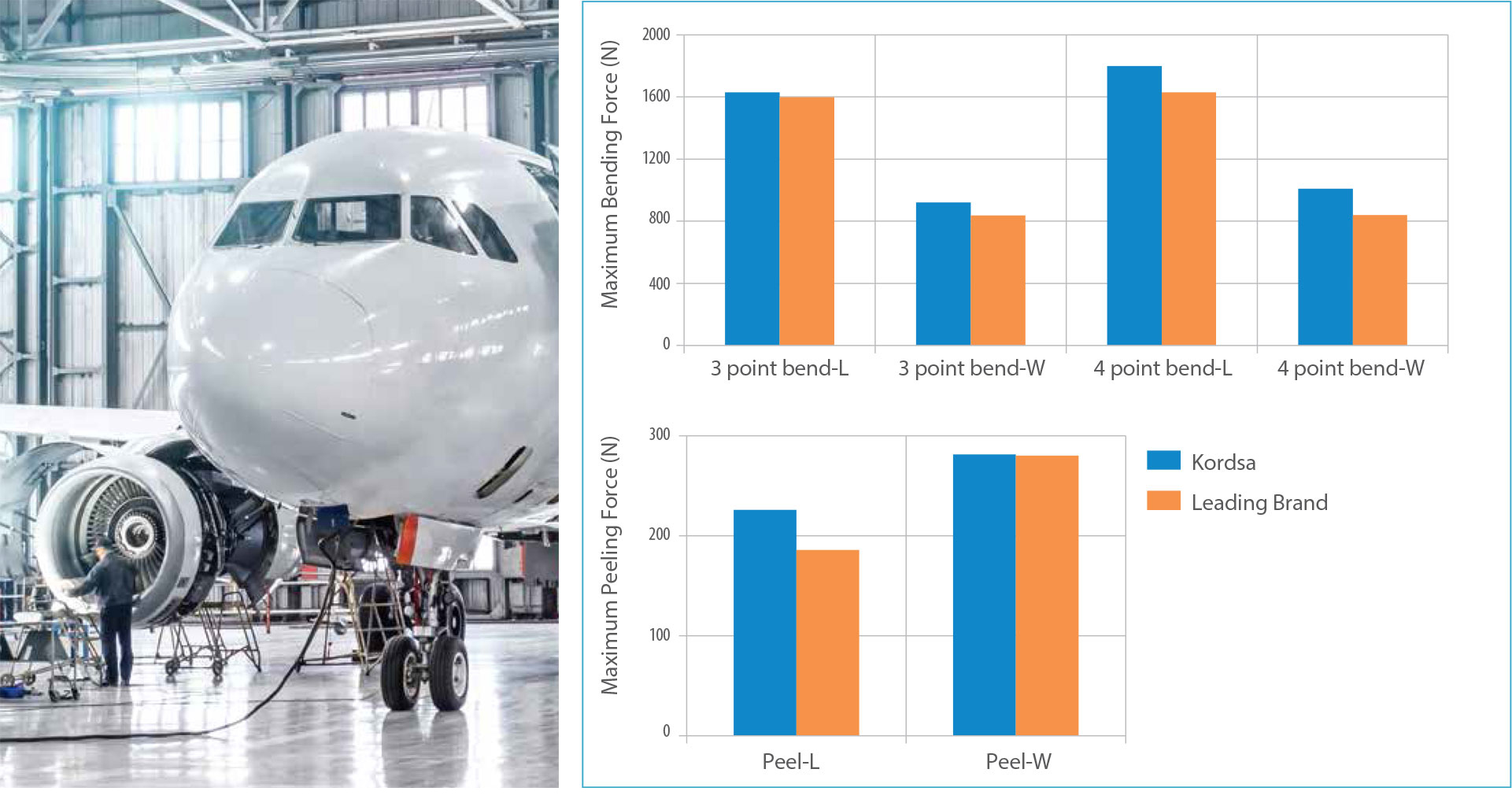
Figure 7 : Comparison of test results with leading brand's commercially availbe product
CONCLUSION
This article has briefly described composite materials and the requirements of composite sandwich panels, as well as giving some simple theoretical background. It has also introduced the development period for KordSA’s composite sandwich panel product. Clearly, the current mechanical test results prove that, in a period of just 6 months, KordSA has developed a successful product with efficient production process parameters. The next step is the rapid commercialization of the product, so that it can become one of the first products to make its mark in the statistical reports about the use of composite materials in aeroplanes.
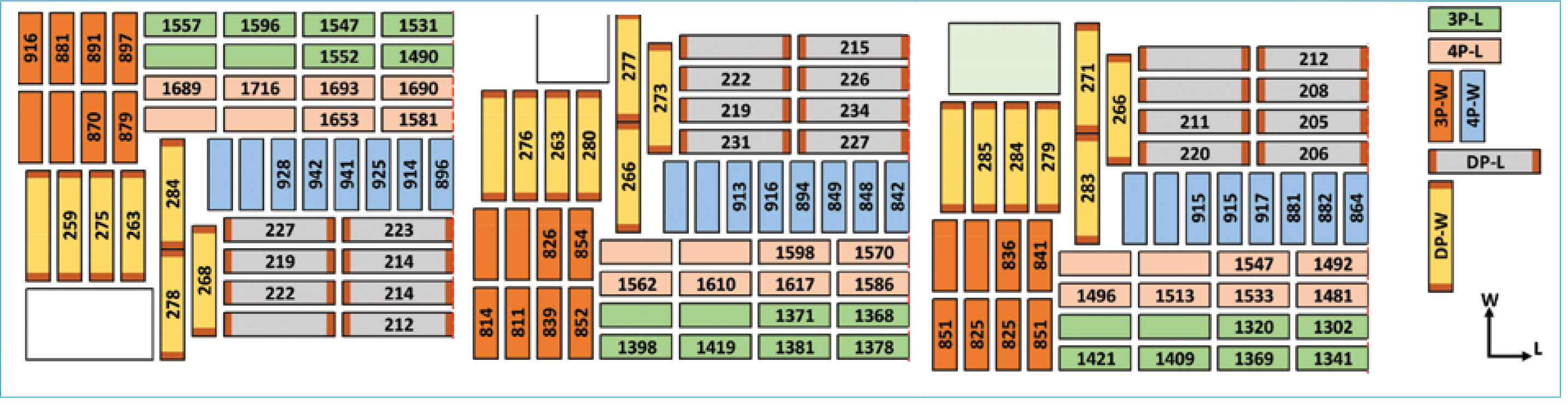
Figure 8 : Maximum loads of each test from different region of the sandwich panel.
REFERENCES
1. Justin Hale, “Boeing 787 from the Ground Up” link
2. Ashby, M., “Material and process charts”, The CES EduPack Resource Booklet 2, p. 42, 2010