Schneider Electric Explains the Impact of Digital Transformation on Production and the Economy
“Digitalization and energy are like the two sides of the same coin”
Digitalization and energy are like the two sides of the same coin; very much conjoined. One can not fully evolve without the other. There is a transformation in this field towards de-centralization because the new internet architecture will be a combination of cloud and edge technologies. And the new energy industry is transforming into micro grids, de-centralized, cheaper and more sustainable energy.
Mr. Bora Tuncer, Schneider Electric Turkey, Iran and Central Asia Cluster President, and a global expert in energy management and automation, explains Schneider Electric’s take on the major concepts of the era: Industry 4.0 and Internet of Things (IoT) as well as Schneider Electric’s efforts in this area.
“Industry 4.0 is efficiency born from the union of manufacturing and information technologies”
As a global company making innovation for 180 years, Schneider Electric quickly integrates all opportunities technology has to offer to its systems. By extension, we are a close follower of the 4th industrial revolution – the 4th revolution after the previous three, namely mechanization, serial production and automation – keeping abreast of technological advancements. At Schneider Electric, we view the 4th Industrial Revolution, that is Industry 4.0 and the Internet of Things (IoT), not so much as a revolution but as an evolution. And for us, the changes and transformation they bring are a natural reflection of the technological developments which impact every aspect of our lives.
Bidirectional communication of smart devices, which forms the basis of Industry 4.0, is not a novel concept. Devices have for the past five decades been able to sense, generate and transmit data. To illustrate, Schneider Electric invented the first Programmable Logic Controllers (PLC) in 1968. Similarly, concepts such as smart controllers, robotic applications, smart sensors, big data, cloud computing and cyber security have for long materialized in many aspects of industry and daily lives. These technological developments have turned devices, which previously communicated only locally, into global-scale data exchangers.
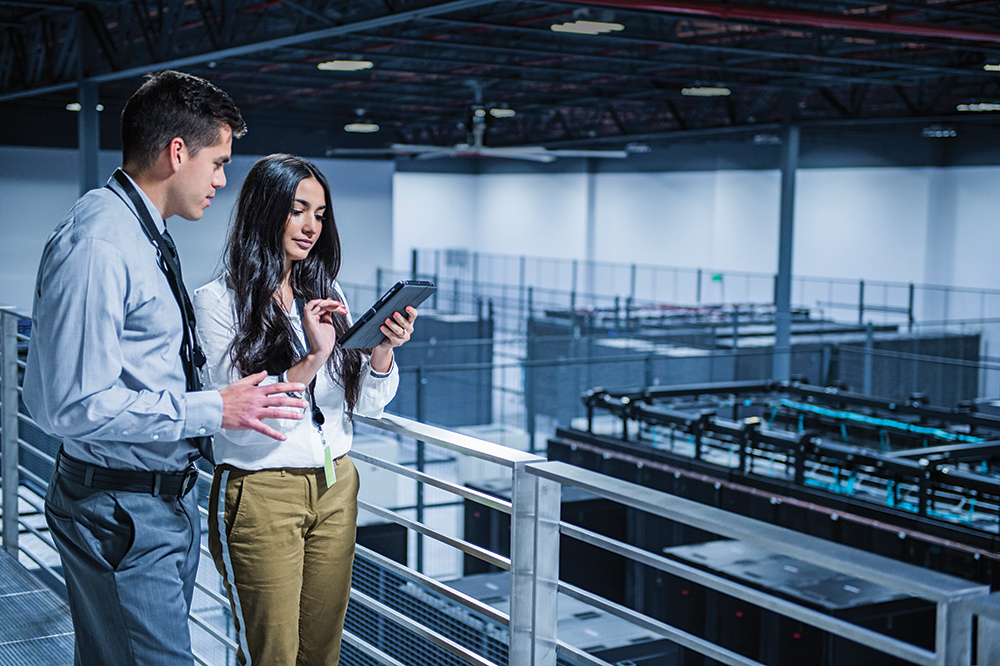
Thanks to the rapid uptake of smart phones and social media, information technologies have become accessible to consumers over the past years. While the effect of billions of internet-connected consumers reached gigantic proportions, another tech mega trend was making its way through: the “Internet of Things,” which includes smart and connected machines.
In this context, the Internet of Things is viewed as an evolution, and has, for some time now been continuing to evolve. Remote monitoring and control has for long been relying on the automation of “things,” while the fundamental difference between that and the “Internet of Things” is the sheer number of data-generating devices connected to the internet. The fact that the cost of the IP infrastructure feature fell quite dramatically paved way for all types of devices to be connected. The forecast is that 50 billion “things” will become connected to the internet by 2020.
All this interconnectedness of things creates an enormous pool of data. Thanks to smart controllers, which analyze aforementioned data and make real-time decisions, we can obtain efficiency and flexibility with a minimum margin of error in an infinite number of areas – from manufacturing processes and supply chain to energy distribution and building management. Manufacturers can thus follow what customers demand more closely.
As a result of this evolution, Industry 4.0, is the real-time and big-data based optimization of the entire chain of values in an establishment – from sales to shipment, even to post-sales – under a single roof. In fact, such optimization does not have to be confined to a single establishment, but can bring together collaborating business partners (subsidiary industry, 3PL, etc.) on the same backbone to boost jointly-offered services and efficiency.
At Schneider Electric, we develop products and services in this field under the name of EcoStruxure, in a way that they incorporate all the layers of an Industry 4.0 application. Our solutions under the EcoStruxure architecture are offered in three layers: Internet-connected products, local control (edge control), and applications and services. Leveraging our breadth of know-how in the market and experience in applications, we offer solutions in the six business lines on our target: Building, Power, Data Center, Machine, Plant, and Grid. The EcoStruxure platform enables the interconnection of everything in an establishment between the manufacturing department and the management floor, critical data collection from sensors and the cloud, analyses of the data to create sensible content, and allows to close this cycle with real-time, actionable data. The platform forms the backbone of the technology on which Schneider Electric builds its solutions it offers to users.
“Internet of Things (IoT) is not about the number of internet-connected objects or machines, it’s about bringing people, processes, data, and things together on a seamless network.”
To the question of what the future may bring regarding IoT, internet-connected smart tools and machinery will outnumber people using the internet in the near future according to tech world’s forecasts. It is expected that in 2020, nearly 30 billion smart objects will be connected to internet covering everything from smart machines and sensors used in industry to micro sensors used in textiles or packaging.
But the important point here is not the number of objects or machines connected to internet; but that people, processes, data and things will be brought together on a seamless network; because, beyond being connected, this is the only way for valid information to reach the right people at the right time so that Internet of Things can create real value.
As much as we need smart machines and connectedness, we also need software that is able to make big data analyses, and that creates meaningful information from the data at hand. At Schneider Electric we develop solutions with this critical need in mind.
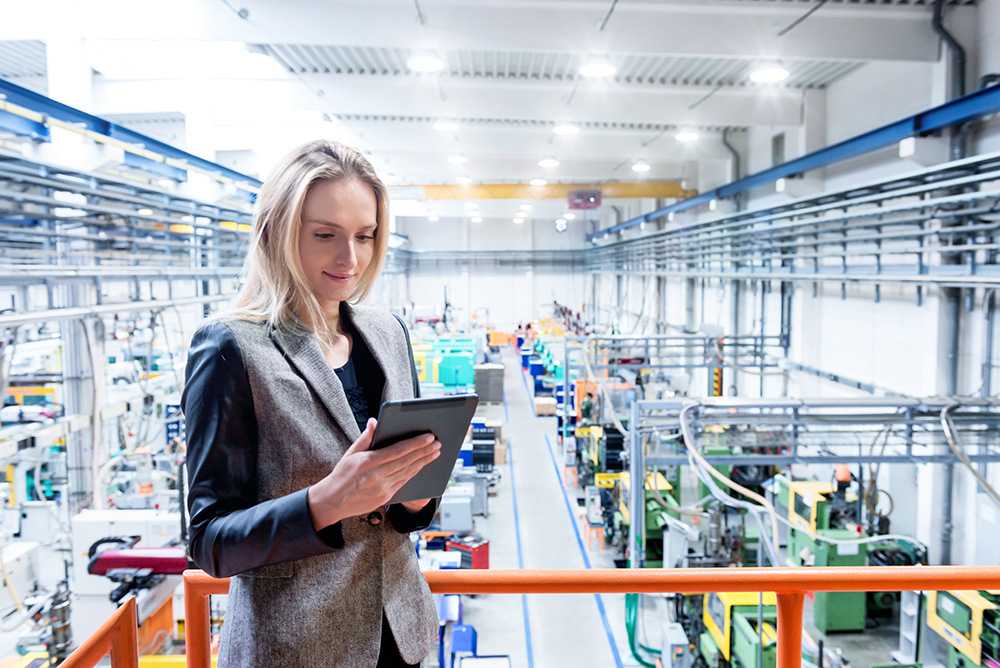
Must invest in technology to achieve economic development in Turkey
Parallel to the process of transformation, which effects the whole world, runs the process of full integration of smart machines and smart factories in big enterprises who think big and who seek global presence. Country-wise, European countries, chiefly among them Germany, and the US have taken some major steps to this end. A host of new generation manufacturing technologies such as the Industrial Internet of Things systems, service-oriented drivers (SOD), and industrial Ethernet networks, which are expected to become widespread manufacturing models of the future, have come to be used.
Turkey, on the other hand, is at the initial stage of this evolution, except large enterprises and big machinery manufacturers. There are no autonomous decision-making mechanisms or integrated plants as such in Turkey. The genes of many fields of science and interdisciplinary studies are waiting to be unified, giving way to technological proliferation.
What makes this transformation inevitable is that the factors underlying the competitiveness of the Turkish industry, such as low labor cost and logistics advantages, will now be under significant pressure. The goal must on the one hand to be to maintain and even improve Turkey’s competitive edge using the Industry 4.0 approach, but more importantly, to create a higher value-added industry in Turkey, which would take a bigger share of the global manufacturing value chain, as underlined in the “TÜSİAD1 Industry 4.0” report, which Schneider Electric supports with our international experience.
To be able to compete in a race the world started two decades ago, an important prerequisite is to invest in technology. It is estimated that based on current prices and size of the economy annually TRY 10-15 billions of investment (ca 1-1.5% of manufacturers’ revenues) is required in the coming decade in order to incorporate Industry 4.0 technologies to manufacturing processes. It would be impossible to compete against the global economy unless Turkey makes such an investment into technology urgently. In this respect, Turkey’s priorities must lay with human resources as well as technology, and investment in education for Turkish companies to develop themselves.
[1] TÜSİAD is Turkish Industry and Business Association.