Significance of Reinforcing of Existing Structures and Usage of Composites for This Purpose
There has been a remarkable increase in the number of people who believe that earthquakes pose a real threat to their lives due to the weak structure of their houses. Most of latter structures are now over 30 years old and in need of urgent structural remedial work. Otherwise, it almost certainly results in loss of life in case of an earthquake. Besides, even if urban transformation was perceived as demolishing and re-constructing within Turkey, technical staff, contractors and municipalities would still be more concerned about reinforcing the buildings owing to both economic and social reasons. It can be undoubtedly said that demolishing, excavating and reconstructing a building would be much more financially taxing and require a much longer time frame than reinforcing a building. Additionally, residents would not want to leave their houses during this period.
For many years, the strengthening or reinforcing of existing concrete structures to resist higher design loads, correct strength loss due to deterioration, correct design or construction deficiencies or increase ductility has traditionally been accomplished using conventional materials and construction techniques but the situations that necessitate reinforcing can be overcome by using composite materials which are known as load carrying materials when used in unison with concrete, steel, masonry and even timber structures. The reasons why composites are being increasingly used as strengthening materials of reinforced concrete elements may be summarized as follows: immunity to corrosion; low weight, resulting in easier application in confined space, elimination of the need for scaffolding and reduction in labor costs; very high tensile strength (both static and long-term, for certain types of FRP materials); stiffness which may be tailored to the design requirements; large deformation capacity; and practically unlimited availability in FRP sizes and FRP geometry and dimensions.
It is a common feeling, among those involved in the application, design, research and development activities in the field of strengthening with fiber-reinforced polymers (FRP), in other words strengthening with composites, that Turkey is developing a strong international reputation both for the value of its contribution in improving the knowledge in this field as well as for the presence of a peculiar and important building heritage. This includes those of historical and architectural relevance as well as more recent masonry, reinforced concrete, pre-stressed concrete, timber structures and steel structures.
Composites in building and infrastructure have a wide range of usage areas as facade, profiles and reinforcing materials throughout the world whereas in Turkey, they are only being used for reinforcing projects in the construction materials market. This method confers a significant advantage over conventional reinforcing methods, which represent concrete, heavy steel or other materials.
The growing interest in FRP systems for strengthening and reinforcing can be attributed to many factors. Although the fibers and resins used in FRP systems are relatively expensive in comparison to traditional strengthening materials, the labor and equipment costs incurred in FRP system installation are often lower. FRP systems can also be used in areas with limited access where traditional techniques would be difficult to implement. After the Kocaeli earthquake in 1999, Kordsa’s warehouses and other buildings at the production site were unfortunately damaged due to the seismic loads. Reinforcing material was chosen as steel plate because this material was unique at that time. Choosing steel as material introduced drawbacks such as the increased weight of steel; the steel plates must be welded together; resulting in a considerable increase in overall thickness due to the protective jacket of concrete. To add to that, being heavier than the composites leads to more labor, power and quality problems when reinforcing a concrete member that has a complex geometry. It is not easy to form steel plates as needed whereas composites can be manufactured in the desired shape and the concrete can be wrapped perfectly.
APPLICATION
There are various types of manufacturing processes that include Hand Lay-up/Spray-up, Resin Transfer Molding (RTM), Compression Molding, Injection Molding, Reinforced Reaction Injection Molding (RRIM), Pultrusion, Filament Winding, Vacuum Assisted RTM (Va-RTM), Centrifugal Casting. Each of which is specialized for a target industry with different purposes such as structural or aesthetic. In the construction sector, the basic FRP strengthening technique, which is most widely applied, involves the manual application of either hand lay-up or cold cured prefabricated systems (pultrusion) by using only adhesive bonding because concrete or any other load bearing member’s geometry can be utterly complex. Also, less equipment, less energy and time should be used. Common in these techniques is having the external reinforcement bonded onto the concrete surface with the fibres as parallel as practically possible to the direction of principal tensile stresses. The hand lay-up technique is the most popular one because pultrusion is not suitable to properly wrap rectangular or square shaped cross-sections while reinforcing by hand lay-up, whole areas of beams and columns are fully covered and strengthened. Thus, pultrusion does not substitute hand lay-up.
Process characteristics of hand lay-up are given below;
- MAX SIZE: Unlimited
- PART GEOMETRY: Simple - Complex
- PRODUCTION VOLUME: Low - Medium
- CYCLE TIME: Slow
- SURFACE FINISH: Good - Excellent
- TOOLING COST: Low
- EQUIPMENT COST: Low
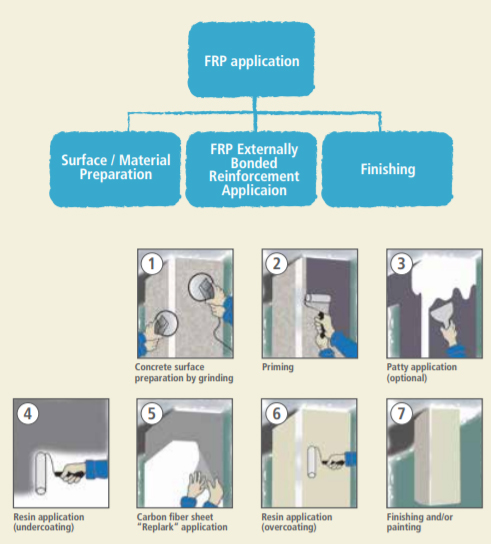
Reinforcing a building by hand lay-up means that dry fabric is laminated with thermoplastic or thermoset resins. In general, two components (epoxy resin-hardener) have been used because of their physical and mechanical properties and bonding capabilities with fiber. To enhance the reinforcing level, carbon fibers are commonly preferred. Fibers can also be selected among boron, glass, aramid, and even polyolefin groups but carbon fibers have outstanding mechanical properties under tension stresses. Therefore, they are preferred notwithstanding the relatively higher cost. Meanwhile, the fabric’s structure should be unidirectional (UD). This is only because of load transfer mechanics among the layers.
Installation steps of carbon fiber reinforced polymers are given as follows;
Surface preparation is paramount, at least lamination of fabric or curing processes. If detected, weak concrete and contaminations, roughened surfaces, rounded corners should be removed and made dust free because the bond quality is influenced by the condition of the existing concrete. Rounding corners to a radius of at least 30mm is an indispensable part of this process providing a uniform load distribution. For this reason, excessive stresses are transferred to the FRP layers in the pointed corners of the section.
If the reinforced concrete surface has surface defects due to the low compacting effort in casting of the concrete, the surfaces are filled and smoothed with epoxy putty having a thixotropic characteristic. After this step, there should be no gap between the reinforced concrete and CFRP layers.
After the primer and putty application and the material preparation (cutting of fabric and weighing of epoxy), application of fiber reinforced polymer can be started. In this step, the epoxy and hardener mixture are applied to the fabric to laminate it hence removing the air gaps between the fabric and the concrete. Removing air from the composite layers is essential in reducing the load transfer between composite layers and/or concrete. Because of the innate characteristics of the hand lay-up method, from time to time, impregnation could be insufficient (delamination of plies, debonding from the surface, etc.) Therefore, special hand tools are used for this purpose.
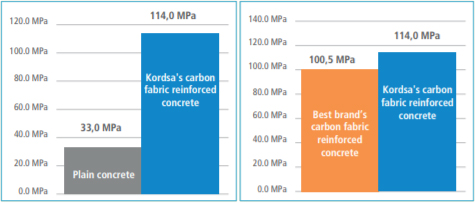
TESTING AND DESIGNING OF COMPOSITES
Basically, the CFRP layers are beneficial in terms of load carrying in three ways; confinement, flexural contribution and shear contribution. One important application of FRP composites is as wraps or jackets for the confinement of reinforced concrete (RC) columns for enhanced strength and ductility. In FRP-confined concrete subject to axial compression, the FRP is principally loaded in hoop tension while the concrete is loaded in tri-axial compression, so that both materials strengths are taken advantage of. Both the strength and the ultimate strain of concrete can be greatly enhanced as a result of CFRP (Carbon fiber reinforced polymer) confinement, while the high tensile strength of CFRP can be fully utilised. Instead of the brittle behaviour exhibited by both materials, CFRP confined concrete possesses greatly enhanced ductility.
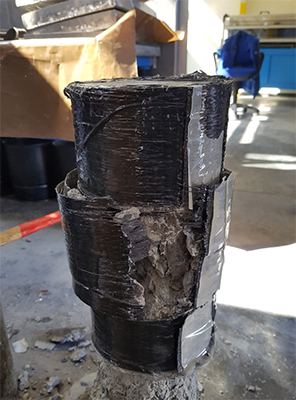
Figure 1: CFRP reinforced cylinder concrete sample, after compression test
It is obvious that after wrapping with CFRP materials the concrete samples undergo a massive change in their load bearing capacity. As seen in Figure, owing to the changing boundary conditions of concrete members after more than one ply of CFRP, their compressive load bearing capacity has improved up to almost 3,5 times. Moreover, when comparing Kordsa’s fabric and the best fabric on the market, a 12% difference can be distinguished.
The second crucial application of FRP composites is the increasing load bearing capacity of concrete members under bending forces for enhanced strength and ductility. In CFRP-confined concrete subject to bending moment, the CFRP is principally loaded in hoop tension again as confined sections. To measure the flexural contribution as mentioned in introduction how effective CFRP layers, ASTM C 1609 tests were carried out.
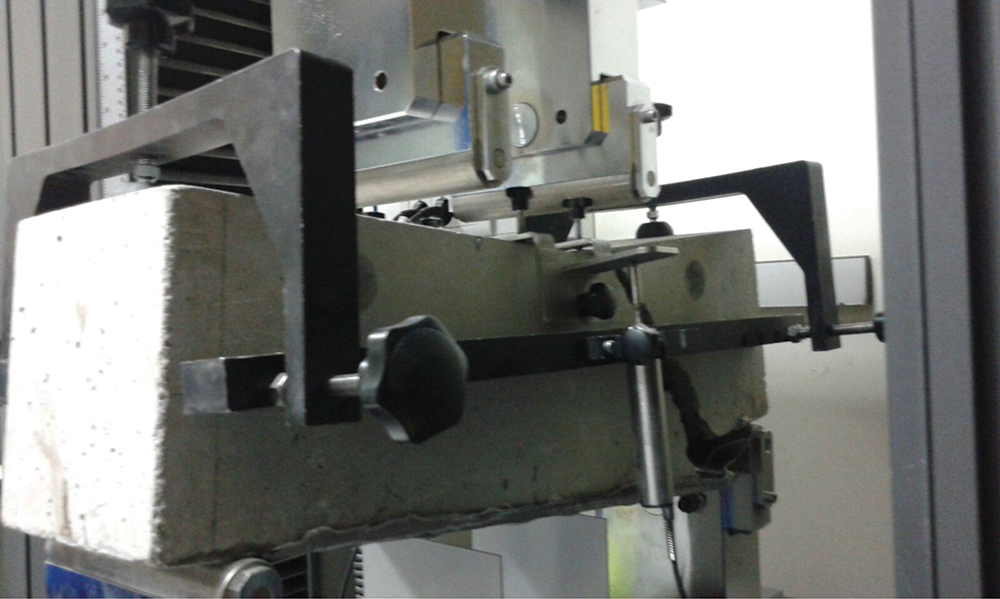
Figure 2: Bending test of CFRP reinforced concrete prism sample
The test results reveal that CFRP materials that are externally bonded to any surface show outstanding performance as seen in the graph. The green circle represents the point at which the concrete cracks. It is almost the same level for all concrete samples including those reinforced by fiber or composite materials in terms of deflection and bending force. The difference between both plain concrete-CFRP reinforced concrete and fiber reinforced concrete and CFRP reinforced concrete can be easily comprehended.
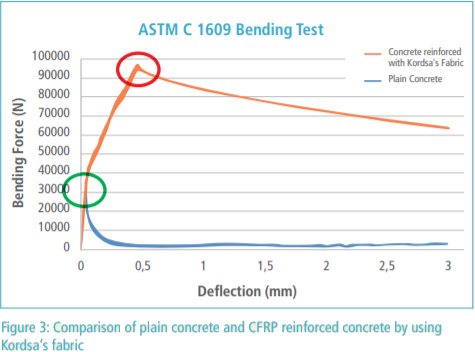
As for red circle, it is the point that CFRP layers start to separate from the concrete surface. The bending force-deflection curve of CFRP reinforced concrete (orange line in graph) would continue to climb up to the end of the test in case of using dowels.
There are various failure modes of FRP reinforced concrete but a critical issue unites all of them at the same point. As seen below with different figures, FRP layers tend to debond from a concrete surface without any deformation on them because of the fact that they are strong enough whereas concrete starts to crack and propagates.
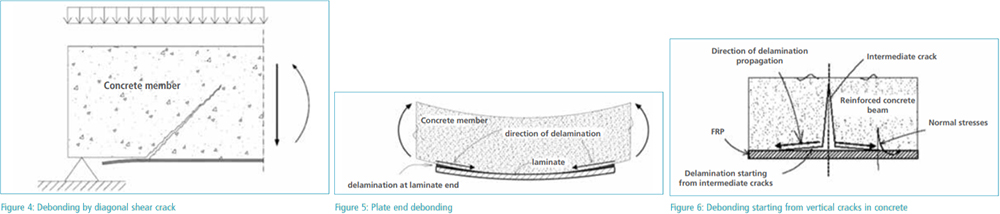
ASTM, ISO and EN tests related to reinforcement of a building are possible to be carried out in Kordsa’s R&D Center, Izmit and Composite Technologies Center of Excellence, Istanbul (Kompozit Teknolojjler Mükemmeliyet Merkezi), Istanbul is well equipped with test devices with the purpose of developing composite materials. Results from any test including composite coupon test and composite reinforced concrete tests, Kordsa’s carbon fabric shows at least 10% better performance without increasing the cost of product.
A carbon fabric and epoxy kit have been developed within a project, along with Construction and Composite reinforcement platforms. After lab scale studies, a full scale application has been done to reinforce a concrete slab and its beam. The design of the in-situ application of CFRP (number of plies, reinforcing type and thickness of composite) has been done by Construction R&D team. Laboratory test results also shed light on the design aspect of the level of carbon fabric’s load bearing capacity. The most frequently used algorithm throughout the world, Guide for the Design and Construction of Externally Bonded FRP Systems for Strengthening Concrete Structures ACI 440.2R, was followed to determine the reinforcement. The shear contribution of the CFRP can be then calculated from equations in this guide; shear force capacity is increased approximately 40 tones-f with the application just 2 plies of composite.
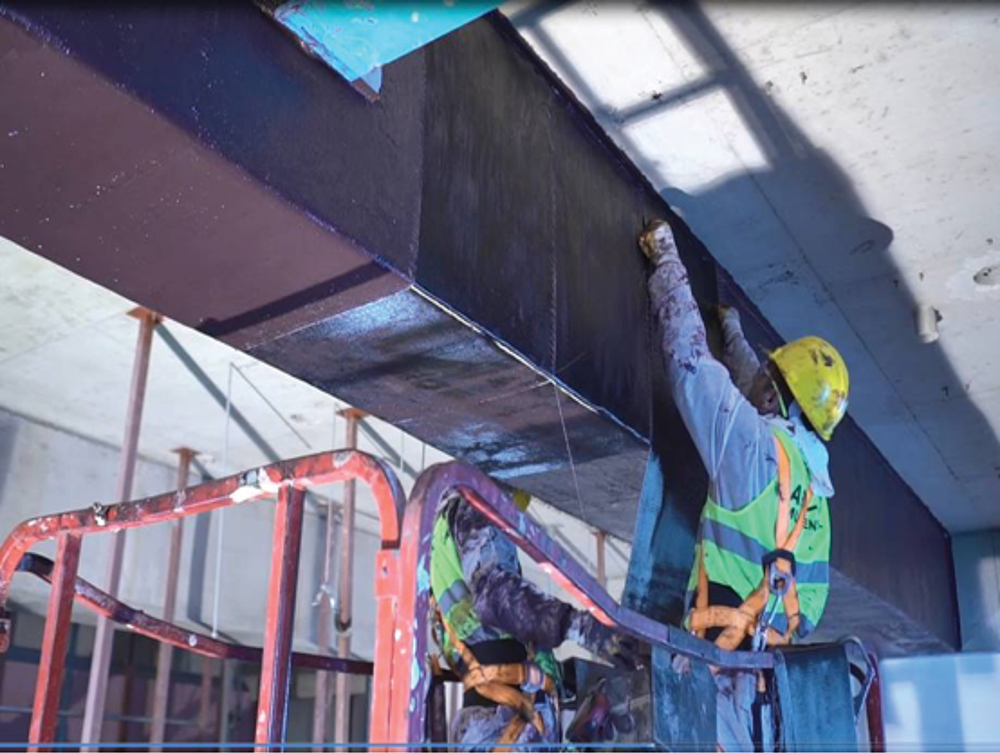
Figure 7: A full-scale application, reinforcing of a concrete beam
According to the voice of a potential customer and end user, Kordsa is found more advantageous than other companies that sell the same sorts of products in terms of lead time, sustainability of quality, onsite user friendliness during application. Manufacturing fabric in Kocaeli means reducing delivering time by 8 compared to importing it from other countries. Korea and China dominate the market but in general end users frequently face quality problems. This material is being installed to reinforce buildings and to save lives. Therefore, the best quality must be sustained for CFRP materials.
Concluding from lab scale studies over a three-year period and field application, it can be said that a new carbon fabric has been successfully created for a reinforcing field and are ready to be brought to the market. To sum up, Kordsa’s carbon fabric is herein applicable for load carrying in accordance with ACI, Eurocode and Turkish Earthquake Code.
FUTURE WORKS
No company in Turkey and only a limited number of companies throughout the world can manufacture prepregs and pultruded sections, especially thermoplastic ones for construction materials. Thanks to playing manufacturer, innovator and leading roles in construction and composite materials fields, Kordsa will pioneer other materials and technologies. The presence of sufficient R&D facilities, knowledge, textile producing experience help us to reach targets. In other words, Kordsa will continue to reinforce every aspect of life.